Hoвocmu CAD/CAM/CAE Разработка Анализ литья Оснастка Производство Сервис Форум





| |
Главная | PTC | Moldflow | Рабочие станции
Многолетнее исследование рынка
CAD/CAM/CAE
продуктов с целью
приме-
нения в разработке и
производстве изделий из пластмасс
привело к выбору
в пользу программных
продуктов широко известных на этом рынке
компаний
Moldflow и
Parametric Technology
Corporation (PTC).
Именно эти
программные продукты являются наиболее
интегрированными между собой и
перекрывают весь мыслимый и немыслимый
диапазон задач которые могут возникнуть
во время создания и производства нового
изделия. Кроме того, обладают интуитивно
понятным CASE
интерфейсом,
единой
удобной системой
манипуляции трёхмерными объектами,
рациона-льным использованием системных
ресурсов, предоставляют возможность
строить трёхмерные объекты легко и
быстро, в то же время не позволяя
допускать ошибки на всех этапах
построения объекта.
Сквозная автоматизация
проектирования и производства достигаемая комплексным
использованием программных
продуктов
Moldflow
и PTC
отлично демонстрируется
на примере создания
сборочного узла
легкового автомобиля на
АО "Владимирский завод "Автоприбор""
(г.Владимир).
Рис.1 Проработка
внешнего дизайна изделия. |
Этап
1
Концептуальное
проектирование дизайна
изделия и общей компоновки
облицовки салона
автомобиля в
модуле Pro/DESIGNER.
Здесь, в основном,
учитываются эстетические факторы и
эргономика. На рис. 1 приведены
некоторые рассмотренные варианты дизайна
внешних обводов.
Выбранный и согласованный с заказчиком
базовый вариант дизайна передается в
среду трёхмерного
параметрического проектирования
Pro/ENGINEER
для дальнейших
конструкторских разработок. |
Этап 2
Проектирование трёхмерной
параметрической геометрии деталей сборочного
узла.
(см.
рис. 2 и 3).
Проектирование
выполняется при
помощи специализированных
конструкторских модулей Pro/ENGINEER -
Pro/FEATURE, Pro/SURFACE, Pro/ASSEMBLY.
Полученная трёхмерная сборка
проверяется
на
отсутствие взаимопересечения деталей
и
соответствие полученных зазоров и
натягов. |
Рис.2
Сборочный узел. |
Этап 3
Рис.3
Чертеж детали. |
Разработка
полного комплекта
рабочих чертежей
на базе принятой
трёхмерной
геометрии.
Виды, сечения и разрезы
на чертежах строятся и образмериваются
автоматически средствами модуля
Pro/DETAIL.
Pro/ENGINEER обеспечивает полную
ассоциативность между трёхмерной
параметрической геометрией
детали или сборки
и чертежами -
любые изменения в трёхмерных
моделях автоматически отображаются в
чертежах и наоборот. Данная особенность
позволяет избежать многочисленных ошибок
при подготовке производства, а также в
процессе его сопровождения.
Следует отметить, что
чертежи в Pro/ENGINEER оформляются в
строгом соответствии с ЕСКД. |
Этап 4
Анализ литья
деталей из пластмассы
с
помощью программных продуктов
Moldflow.
Исследование процессов
литья деталей
проводится в
программе
Mold
adviser комплекса
программ фирмы
Moldflow.
Определяются наилучшее расположение
впускных литников, время впрыска, распределение
давления,
температура, возникающие напряжения, расположение
линий холодного спая, время
охлаждения, возможные
утяжины, необходимое усилие смыкания
литейной машины .
При
необходимости в более мощном продукте
Moldflow Plastics Insight (MPI) проводится оптимизация
литниковой системы
(MPI/Flow), анализ
охлаждения литформы (MPI/Cool), анализ
усадки и коробления (MPI/Warp), анализ исполнительных
размеров ФОД (MPI/Shrink), анализ
ориентации волокна (MPI/Fiber),
автоматическая оптимизация
технологического режима (MPI/Optim),
анализ поведения изделия
при эксплуатации (MPI/Stress);
анализ литья с газом (MPI/Gas).
На рис.4
показаны результаты анализа
детали на наличие
линий холодного спая
в зависимости от
расположения литников.
Этап 5
Проектирование технологической оснастки
для литья деталей . |
а)
линии холодного спая в опасных сечениях
детали;

б) линии холодного спая
вне опасных сечений детали
Рис.4
Оптимизация расположения линий холодного спая в
детали. |
На основе полученных на
2 этапе трёхмерных моделей
деталей сборки
в модуле Pro/MOLDESIGN
автоматически
генерируются формообразующие
элементы
литьевых форм с
учетом усадки материала,
линий разъема,
литейных уклонов и радиусов. Проводится
анализ извлекаемости отливок
из
литьевой формы.
Далее выполняется
окончательная
трёхмерная
сборка
литьевой формы - в стандартный блок формы
вставляются толкатели,
опоры и
т.д.,
ассоциативно оформляются соответствующие
чертежи - см. рис.5.
а)
трёхмерная модель
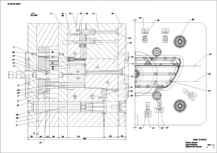
б) сборочный чертеж
Рис.5
Модель литьевой формы
и сборочный чертеж |
Замечательная особенность
ядра
Pro/ENGINEER- полная ассоциативность,
позволяет автомати-чески
отображать все изменения элементов
геометрии деталей
изделия производимые в процессе
проектирования,
корректировки изделия и
доводки.
Действует и обратная связь. Так, при
проведенном изменении кривой сопряжения
деталей в трёхмерной
модели сборочного узла
(см. рис.2) соответствующим
образом корректно изменились
формообразую-щие
поверхности литьевых форм этих деталей,
что исключило трудоемкие процессы
проверок
и корректировок, а также особенно
трудоемкие процессы слесарной доводки
оснастки после получения пробных отливок.
Сквозное
проектирование в Pro/ENGINEER сокращает
время изготовления
оснастки и значительно повышает качество
изделий. Оценка такого сокращения
времени изготовления приведена ниже. |
Этап 6
Получение
управляющих программ для станков с ЧПУ,
по которым обрабатываются
формообразующие поверхности литьевых
форм.
По трёхмерной
геометрии пуансонов и матриц литьевых форм,
спроектированных на этапе
5 (см. рис.5), в модуле Pro/MFG автоматически
строятся управляющие программы фрезерной
и электро-эрозионной
обработки. До вывода
программ на станок проводится
визуальный контроль движения инструмента,
проводятся необходимые корректи-ровки по параметрам
инструмента, режимам обработки (рис.6).
Полная ассоциативность в
Pro/ENGINEER обеспечивает автоматическое
изменение управляющих программ станка по
проводимым изменениям в трёхмерной геометрии
детали или
по изменениям в оснастке.
Такая ассоциативность окончательно
дополняет информационное единство
процессов конструкторского и
технологического проектирования в
Pro/ENGINEER. |
Рис.6
Моделирование фрезерной обработки пуансона литьевой формы. |
Этап 7
Изготовление
пуансонов и матриц литьевых форм.
Рис.7
Изготовленный на фрезерном станке с ЧПУ
пуасон. |
Полученные на 6
этапе программы для
станков с ЧПУ
преобразуются в
коды металлообрабатывающих
станков в модуле Pro/NC-POST. Далее
следует процесс непосредственной обработки
формообразующих элементов оснастки. На
рис. 7 показана
фотография готового пуансона литьевой формы. После
достигнутой посредством Pro/ENGINEER
высокой точности обработки, пуансон практически
не нуждается в
дополнительной слесарной доводке. |
Описанные с 1 по 7 этапы полностью характеризуют
сквозной процесс автоматизированного
проектирования и изготовления
различных изделий,
обеспечивающий их высокое качество и
резкое сокращение сроков производства.
Рис.8
Сквозное автоматизированное
проектирование и изготовление
изделий на основе
комплексного подхода в АО "Владимирский
завод "Автоприбор"".
Аналогичная структура
диаграмм характерна и
для остальных деталей
сборочного узла(см.
рис.2). |
Структуру этого процесса наглядно
иллюстрирует рис.8.
Cокращение сроков
производства готовых изделий
по сравнению с традиционными
ручными процес-сами отражено в сравнительных диаграммах на рис.9. |
Анализ диаграммы по
традиционным процессам (рис.
9а) показывает,
что конструкторская и технологическая
подготовка производства составляют всего
6% от общей трудоемкости
производственного процесса
изделия, а собственно производство - 94%
(52%-изготовление литьевых форм на
станках, 42% - слесарные доработки). |
Рис.9
Сравнительная трудоемкость
изготовления
традиционными
методами и
методом сквозного
автоматизированного
производства. |
Следовательно, эффективность внедрения
системы сквозного автоматизиро-ванного проектирования
и производства определяется отнюдь не
сокра-щением
персонала конструкторов и технологов (их
вклад в общую трудо-емкость
всего 6%), а созданием такого уровня
компьютерной оснащенности их работы по
подготовке производства, при котором
резко уменьшится трудоемкость
производства (вклад производства в общую
трудоемкость - 94%). Реализация
сквозной автоматизации обеспечивает
решение главной задачи - сокращение
сроков создания изделия (в 5.5 раз - см.
рис.9 а и б) при
обеспечении его высокого качества.
Характерно, что относительная доля
трудоемкости проектирования в
автоматизированном процессе повышается с
6% до 23% (см. рис 9 б), что
свидетельствует о росте
значимости процессов инженерной
подготовки производства с использованием
современных технических и программных
средств САПР.
Предоставленные материалы опубликованы журналом "САПР
и графика".
|
|